Dr Jeannette McGill, Vice President and General Manager of Metals and Mining at AspenTech, explores how digital transformation in the mining industry can enhance the entire value chain.
STRIKING GOLD
Traditionally, the mining sector has been cautious to embrace digital innovation. Frequently operating in remote locations, with poor network bandwidth, limited scalability, and challenging physical terrains, digital transformation and the long-term culture change that comes with it has often been side-lined to prioritise immediate project outputs. Accordingly, BCG’s 2021 Digital Acceleration Index (DAI) reveals that metals and mining businesses are approximately 30-40 percent less digitally mature than comparable industries, such as automotive and chemicals.
However, things now appear to be changing. Post-pandemic pressures, supply chain challenges, and economic uncertainties are causing organisations to rethink how their mining operations are performed. A renewed interest in modern digital technologies has come to the fore – not only as a means of improving efficiency and resilience at a time of economic downturn, but also to gain a stronger long-term competitive edge over more conservative peers.
By accelerating the adoption of automation and digital capabilities to build the agile, secure, and intelligent mines of the future, businesses stand to connect and optimise the entire value chain, quickly delivering return on investment and unlocking long-lasting value both below and above the ground.
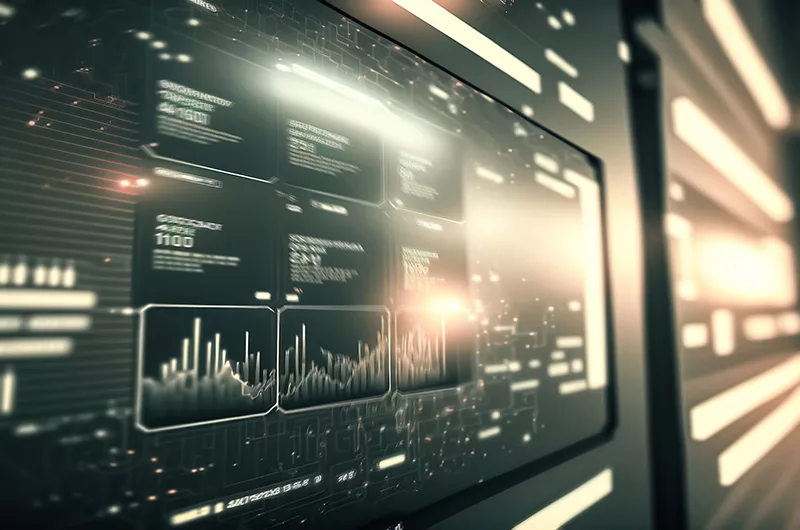
THE DATA-DRIVEN MINE
The success of any mining digital transformation project is influenced by how effective the mechanisms and tools are by which data is moved from one part of the value chain to the next, especially when it comes to aggregating the gathered data to achieve a comprehensive view of how one part of mining operations affects another. Consequently, this data needs to be managed efficiently to support the planning, control, and decision-making that underpins the intelligent mine of the future.
Difficult decisions are made daily by various departments, making it all too easy to operate within isolated data silos. With greater transparency around the impacts of each challenge, mine management can adapt and change course in a way that reduces disruption and maximises productivity, profitability, and predictability.
The mining sector now has an opportunity to implement single solutions that automate data gathering from various processes and facilities, using tools that detect bad data, process it in the correct context, and yield insight in a meaningful and actionable timeframe.
PRESCRIPTIVE MAINTENANCE
But the insight derived from good data is just one piece of the puzzle. Mining companies need to leverage advanced machine learning (ML) technologies to learn from and improve in the future, in order to remain agile and resilient in decades to come.
Traditional maintenance practices often fail to deliver the benchmark equipment availability, performance, and reliability required to shape the varying schedules upon which financial projections and corporate targets are based. This not only impacts quarterly profitability but can also undermine confidence in operational leadership, which has knock-on effects on investor sentiment.
Modern prescriptive maintenance solutions are different. Utilising asset sensor data to proactively monitor equipment for imminent and future failures, the technology empowers companies to collaborate and plan around predicted downtime, rather than having to reactively muddle through it. For example, prescriptive maintenance technology can assess the health of numerous machines every few minutes, delivering insights around equipment performance to maintenance teams, often with prescriptive advice that addresses the bad actors and known issues.
Furthermore, prescriptive maintenance and artificial intelligence (AI)-powered technology is key to integrating, co-ordinating, and optimising the entire value chain, from the extraction of raw materials to the delivery of products to customers. Tailored to suit specific work environments and processes, new technologies are bringing improved operational efficiencies across the board, while also lowering costs. Not only does this help to avoid the lost revenue and profits associated with downtime, but it also gives teams more time to evaluate and prepare, allowing them to get ready for future complex challenges including meeting ambitious net zero targets, and facing increased competition and equipment maintenance costs.
Human interpretation simply isn’t capable of deriving the insights this technology delivers. The applications monitor many variables on behalf of the workers, who receive warnings to help determine which issues to prioritise.
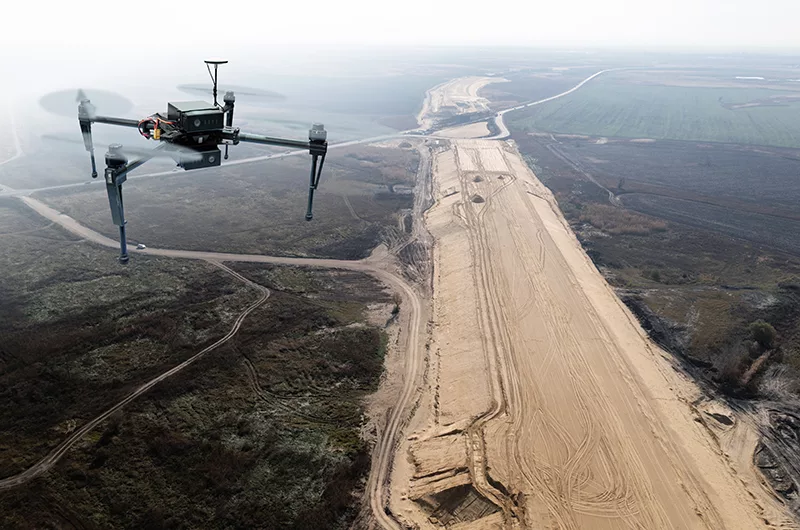
POINTING THE WAY FORWARD
An asset performance management (APM) approach, with integrated prescriptive maintenance capabilities, can support the mining sector in enhancing reliability, availability and uptime while reducing the requirement and expense of redundant equipment.
Operations teams have long planned for lower availability, often installing more machines or truck fleets than they necessarily need. With the right technology, mines can achieve benchmark reliability without the need for more people, more equipment, or higher budgets. Companies can work at the required production levels, consistently delivering to the short-, medium-, and long-term plans and projections that investors and markets demand.
Mines can also implement other aspects of APM programmes to draw on data from sensors and other sources, from enterprise resource planning (ERP) systems and manufacturing execution systems (MES) to laboratory management information systems and advanced process control (APC) systems. Sourcing this data will ultimately benefit the entire value chain, as teams will have the visibility needed to identify bottlenecks, improve troubleshooting, and ensure safer and more profitable end-to-end operations.
ACCELERATING THE DIGITAL JOURNEY
To achieve a truly intelligent mine, the industry must now seize the opportunity to embrace and use digital optimisation technologies. Investing in the right solutions will help mining companies to improve productivity and profitability at scale, resulting in innovative new business models across the entire mining value chain.
Operators that fail to adapt, or are slow to advance on their digital transformation journey, are likely to struggle when competing against more forward-facing businesses. Therefore, prescriptive maintenance applications are increasingly needed to bring fast, measurable results, delivering significant reductions in downtime, reducing safety risks, and ensuring the entire mining operation can meet tomorrow’s challenges with greater efficiency, transparency and agility.