“No mine ever stops over Molycop.” We speak to Michael Parker, President of the company’s Australasian division, about the pride and challenge of keeping Australia’s mining industry turning.
INTRODUCTION
“The manufacturing industry in Australia has always been challenging, however, COVID-19 and other global supply chain disruptions have highlighted the true value of local supply rather than the reliance on long and complicated supply chains for critical products and services.”
Operating at the heart of the mining and rail transport industries, Molycop manufactures specialty steel products in Australia with an established history stretching back over a century and is currently part of the international American Industrial Partners group.
In Australia, the company manufactures products such as railway wheels, industrial fasteners and steel grinding balls that are destined for its mining customers’ grinding mills, where the balls are used to break down rock. Elsewhere in the world Molycop manufactures grinding balls in Canada, USA, Mexico, Peru, Chile, Indonesia and Spain servicing all the major hard rock mining regions.
Michael Parker, Australasian President at the company and orator of the opening statement, has witnessed first-hand the impact of the pandemic on local manufacturing and its ability to maintain supply to the country’s mining and other critical industries.
“The long-term shift to global supply chains has left many businesses exposed and highlighted the real fragility of long and complicated supply chains,” he continues. “It has been an opportunity to really show the value of the Molycop model; it’s built on having people and manufacturing plants located close to the customer, holding greater control of the supply chain and also being able to support customers with training and technical services, as well as digital technology innovations through local expertise.
“People are recognising the value of home-grown suppliers and what they can offer compared to offshore suppliers with their longer supply chains and associated costs. COVID-19, among other things, has really brought this to the forefront. Escalating shipping costs, congested ports, the scarcity of shipping containers are extremely challenging issues to manage for suppliers with long supply chains. Our mining customers demand certainty and transparency over our supply chain and the inventory held within it.”
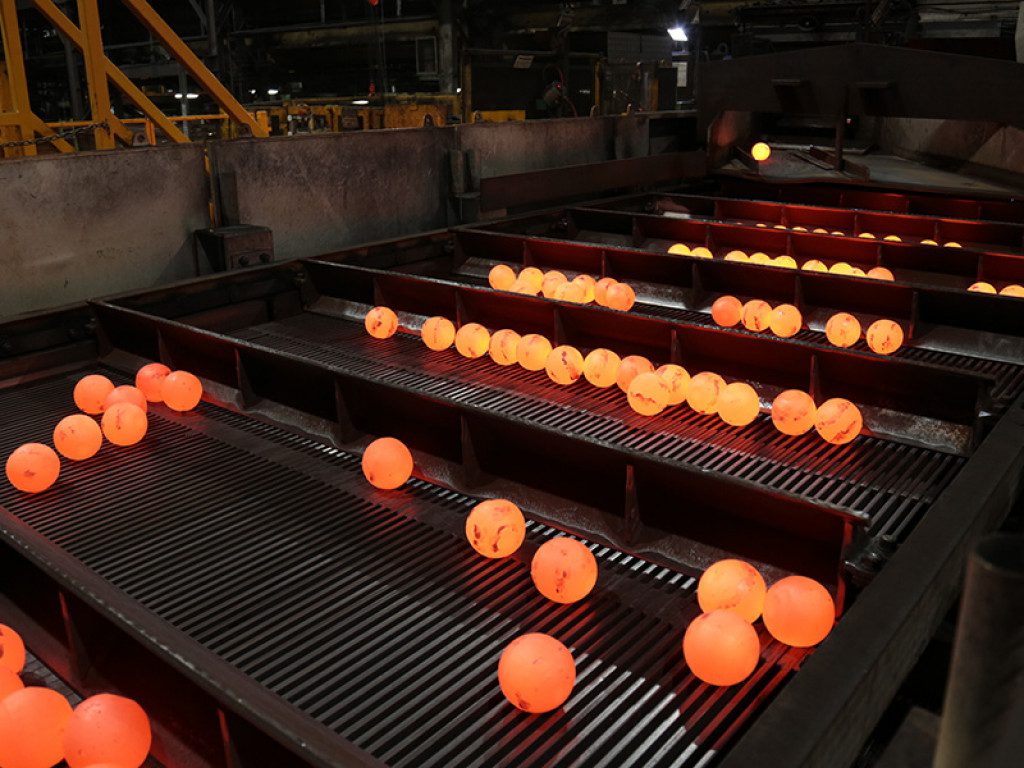
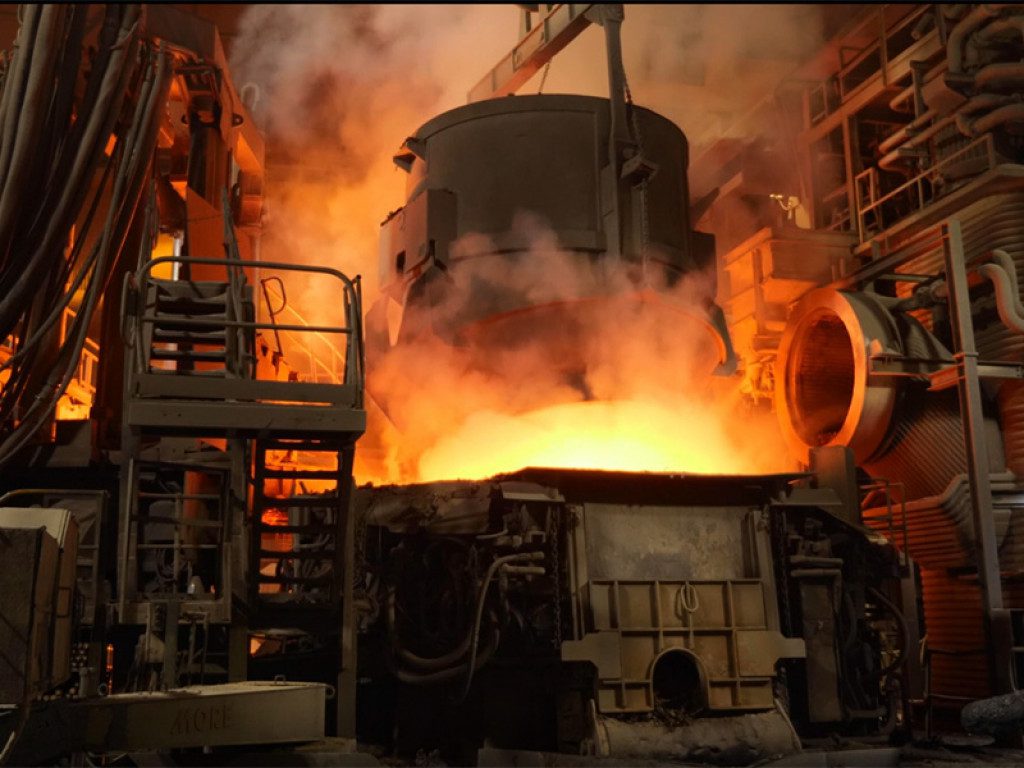
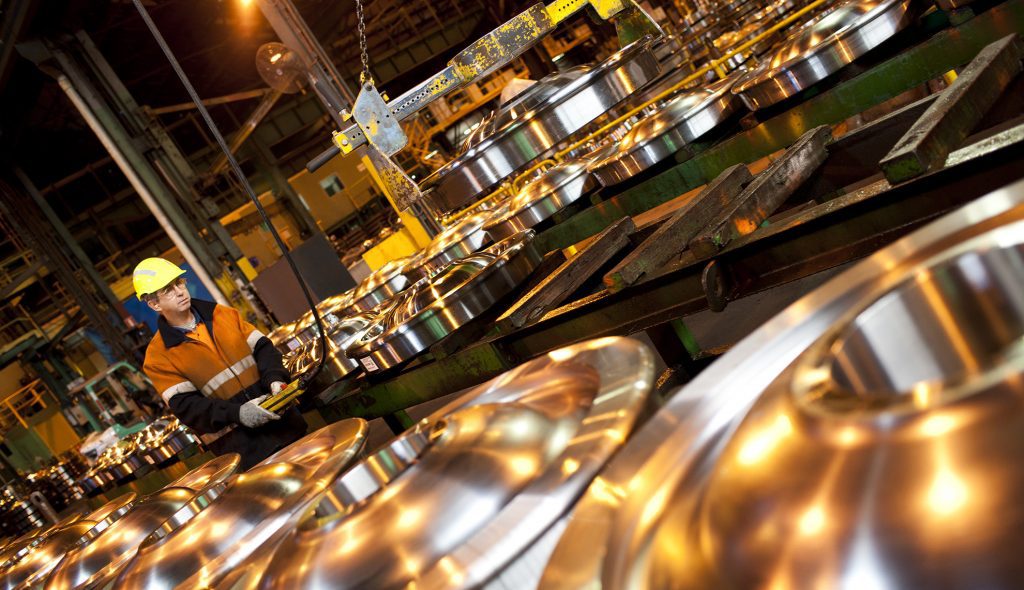
TECHNICAL SERVICES
Technical experience, software, service and support is what sets Molycop apart. The company is able to provide a range of services for both start-up and established mine operations, where its goal is to increase productivity while lowering operating costs for its customers. Molycop’s highly trained team understands the complexities of mining and aims to assist in optimising mineral processing operations by providing solutions that will enhance your overall operation.
“The onset of COVID-19 has highlighted the importance of having locally based technical support teams strategically located close to key mining regions,” Parker explains. “International travel restrictions, introduced to stop the spread of COVID-19, meant that it is important to have your technical support teams based in country. Not only has internal travel been severely restricted, but also the increased testing requirements, safety protocols and quarantine restrictions required to gain access to mine sites means that it is critical to have locally based support capability.”
DIGITAL SOLUTIONS
Molycop’s services are only evolving, providing its customers with the latest innovative solutions in the field of ore crushing, and advancing the efficiency of mining operations to the end benefit of people and the environment.
“The area we are really focusing on is the ability to track mine critical data streams from within our mining customer’s operations using the latest sensor systems,” Parker explains. “This data stream is then analysed in real time to identify or anticipate unfavourable or sub optimal events within our customers’ operations so that they can take the necessary actions to keep the milling circuit fully optimised.”
“The breaking down of large rocks into smaller pieces in these large mills results in a very aggressive internal environment within the mill. Plus, it is very difficult to monitor what is occurring within the mill as cameras and sensors do not survive this violent environment of large rocks and steel balls moving at high speed. To combat this and provide insight into the inner workings of the mill, one of our developments involves embedding a sensor within a steel grinding ball which is introduced inside the mill, as well as placing a number of sensors on the outside of the mill shell and at entry and exits points to the mill. These sensors collectively provide data such as the impact forces within the mill and the motion of the charge which we correlate with overall mill performance to gain a first-hand view of processes from within the mill itself.
“Comminution or the milling of ore consumes around 53 percent of all energy consumption on an entire mine site. That amount of electricity globally across all milling activity amounts to three percent of electricity consumption in the world, which is enough to power Germany for a year,” Parker adds. “There is a lot of energy being consumed, so even small improvements to the energy efficiency of these mills will have a massive impact.”
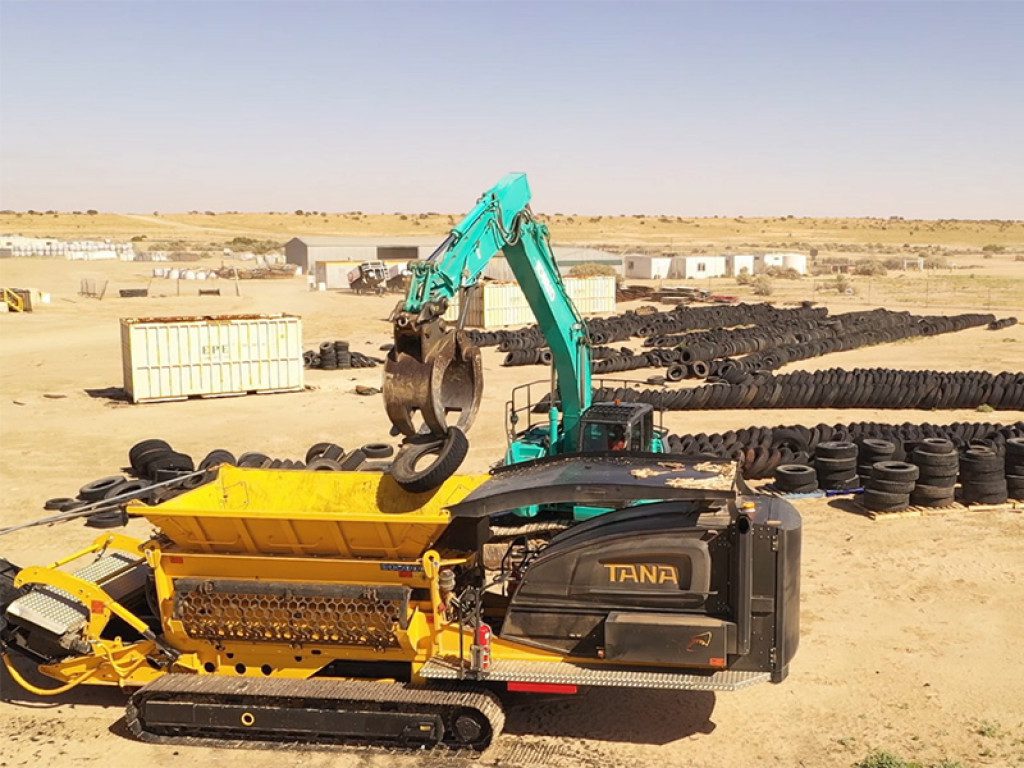
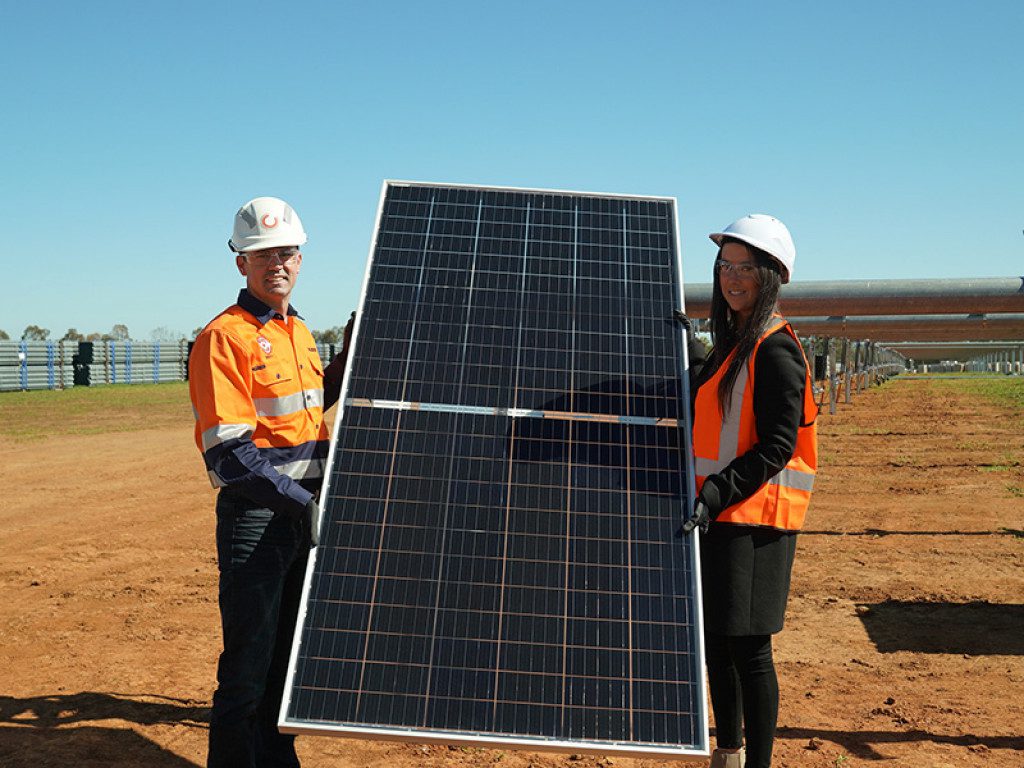
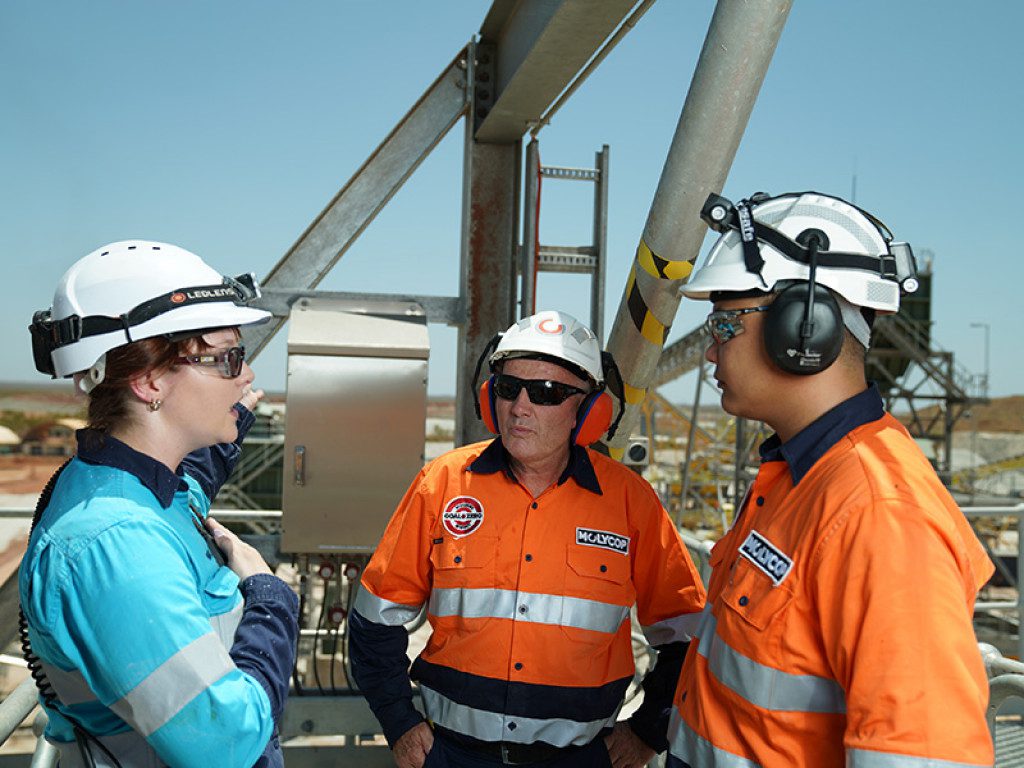
SUSTAINABLE PRODUCTION PROCESS
Molycop is at the forefront of sustainable and responsible steel product manufacturing. Its Electric Arc Furnace (EAF) steelmaking process produces significantly lower carbon emissions than the predominant steelmaking process used by various competitors in the industry.
“Our steel making process uses electrical energy to melt and refine scrap steel, resulting in our steel products being manufactured from over 93 percent recycled materials,” Parker explains.
“This is a really important aspect of how we operate, especially in the face of the pressure caused by resource scarcity globally. For example, we take scrap from old cars, steel springs from mattresses, demolition scrap, rail tracks, tyres, shredded white goods such as refrigerators and spent steel products from our customers, and we recycle and remanufacture these materials into new steel products.”
“Each year our EAF consumes scrap generated from recycling 200,000 cars, steel springs from over 300,000 mattresses and steel wire from two million tyres,” Parker adds.
Inherently EAF steelmaking has carbon emissions about 50 percent lower that the predominant Basic Oxygen Furnace Steelmaking process.
“No mine ever stops over Molycop”Michael Parker, President – Australasia, Molycop
RESOURCE RECOVERY – MOLYCOP 360
In order to improve its capability and commitment towards resource recovery, Molycop has acquired JLW Services, a recycling centre business based in Cootamundra in New South Wales. Rebranded as Molycop 360, it specialises in resource recovery and waste management services for problematic waste streams, including end-of-life mattresses, tyres, conveyor belts, polypipe and intermediate bulk containers (IBCs).
Molycop 360 provides integrated logistics, waste management and resource recovery solutions for businesses, government, councils, and the mining industry and has the capability to either collect material and process at a central location or, typically for remote mining operations, process material on-site. Benefits of on-site processing include more efficient transport costs for any waste and reclaimed materials leaving site as well as reduced waste volume going to landfill. Molycop can also recycle ferrous and polymer materials through its EAF Steelmaking process.
According to Michael Parker, the acquisition of Molycop 360 has placed the company “at the forefront of responsible and sustainable steelmaking and manufacturing. We are committed to building the circular economy, liberating value from waste streams and supporting our customers’ sustainability goals”, a statement that shows the level of dedication Molycopholds towards sustainability from the top-down.
COLLABORATIVE DEVELOPMENT
Over the past decade, Molycop has formed a close partnership with the University of New South Wales (UNSW) SMaRT Research Centre, providing critical industry support in the development and commercialisation of innovative recycling technologies. Through this partnership, Molycop has installed Polymer Injection Technology (PIT) at its EAF facility.
“PIT is a technology developed by the UNSW, invented by Professor Veena Sahajwalla, around 10 years ago,” Parker elaborates. “It is another example of how we try to extract as much from waste streams to recycle as possible.
“In the steel making process you need to use carbon, it’s a fuel, an alloying element and a reducing agent, so it is a necessary component in the steel making process. Historically, we would use imported carbon materials that have been derived from coal or oil, but what PIT allows us to do is substitute around half of that material with recycled polymers (typically end of life, rubber and plastics) that we can now recover and repurpose through our Molycop360 business. This allows us to partly replace a virgin raw material with a repurposed product that would otherwise be destined for landfill or a stockpile somewhere.”
MINING AHEAD
Looking forward, Molycop’s ultimate purpose remains unchanged to support customers through the secure and value adding supply of critical mining consumable products and technical services. Given the lessons from the COVID-19 pandemic and the expected growth in the demand for critical metals such as copper, as the world decarbonises, prudent risk management will require a reassessment of supply chain resilience. Molycop is uniquely positioned to provide customers with the requisite supply chain confidence. “No mine ever stops over Molycop,” Parker affirms.
Molycop’s 100-year track-record has been built on providing the highest quality products and delivering outstanding supply assurance. “We want to help our customers achieve their goals. That is why we are also enhancing our sustainability credentials and digital capabilities. Mining plays a critical role in the growth and prosperity of our society. Molycop is committed to supporting our customers as they liberate the valuable minerals that are fundamental to our everyday life and that will keep society moving forward.”