- THE POWER OF DATA
- Q&A WITH TOM CAWLEY, EXECUTIVE CHAIR AND INTERIM CEO, MAXMINE
- What is the key to a greener, more sustainable future in Australia?
- As a data platform, how does MaxMine improve operational efficiency, profitability, safety, and sustainability?
- How powerful is data in achieving net zero?
- What about the technology trends that are set to revolutionise the mining industry, including AI, geospatial technology, and digital twins?
- What can mining learn from other sectors to reach net zero targets?
- Do you have any tips on decarbonisation strategies and solutions?
THE POWER OF DATA
Cawley has solidified MaxMine’s position as a major player in the mining data sector over the last eight years and is committed to shaping a more sustainable future for generations to come, with a passion for sustainability that sets him apart as he actively engages in various social and environmental causes.
Q&A WITH TOM CAWLEY, EXECUTIVE CHAIR AND INTERIM CEO, MAXMINE
What is the key to a greener, more sustainable future in Australia?
Tom Cawley, Executive Chair and Interim CEO (TC): Diesel use in mining, open-cut mining trucks, diggers, and ancillary equipment represents a high proportion of total energy use in mining countries.
In the case of Australia, it amounts to six percent of total national energy use. Material progress remains slow, and currently, there are only two zero emissions trucks operating in production out of a global mining fleet of 56,000.
The keys to abatement are to start making early progress. Additional measures, including adding new electric hydraulic shovels and blends of low carbon diesels, will enable the near-term target of delivering the first 40 percent of carbon abatements.
To develop zero emission fleets development, it is also key to accelerate testing, build models to determine the best technology solutions for each mine type, and identify early implementation options.
As a data platform, how does MaxMine improve operational efficiency, profitability, safety, and sustainability?
TC: Fleet management systems were initially designed for specific problems; their information collection and data platforms were designed with these specialised applications in mind.
MaxMine took a different approach. From day one, we have collected all sensor data and built a flexible data platform upon which applications are built.
This means MaxMine has the richest dataset in the industry, and the ability to solve a broader range of issues. Specifically, we have over eight million hours of second-by-second data, including fuel flow, across all major original equipment manufacturers (OEMs) and asset types.
This enables equipment use to be broken down on a second-by-second basis, providing feedback to operators, mangers, planners, and maintenance.
It also allows us to build productivity improvement tools enabled by rich data, measure the carbon benefits of improved productivity, target further diesel/carbon reductions, and provide high-relation fuel burn/carbon intensity data to the planning process, to further reduce energy intensity.
We discuss the power of data in achieving net zero, the trends that are set to revolutionise mining, and what the industry can learn to reach sustainability targets.
“MaxMine has the richest dataset in the industry, and the ability to solve a broader range of issues”
Tom Cawley, Executive Chair and Interim CEO, MaxMine
How powerful is data in achieving net zero?
TC: Without data, we cannot measure and improve productivity, or objectively identify and assess the lowest cost abatement pathways for mining, especially mining haul fleets.
What about the technology trends that are set to revolutionise the mining industry, including AI, geospatial technology, and digital twins?
TC: Digital twins that can simulate the practical complexities of mining will be central to identifying and designing the lowest cost abatement pathways, and materially mitigating the risk of implementation.
AI is already in use as a tool for development and management. MaxMine uses automated activity classification to reduce human error in the measurement of fleet activity and performance.
AI presents an opportunity to analyse fleet performance data, summarising human feedback information from operations and many other applications. However, technical debt in existing data platforms will likely act as a barrier to fast up-take.
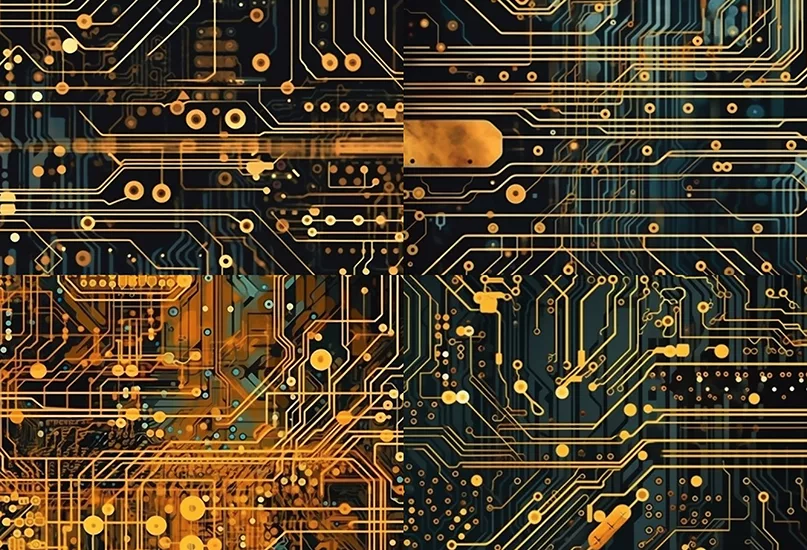
What can mining learn from other sectors to reach net zero targets?
TC: Mining is an operational sector; often the greatest opportunities sit within operational excellence and operating the exiting assets well.
Unlike other sectors, which have high process control, the geology, equipment availability, and human performance in mining is inherently variable. Automation has been hard to perfect and scale, whilst autonomy in mining trucks is still in the two to three percent range, with limited autonomy on other major equipment.
Whereas other sectors, such as manufacturing, have achieved high operational consistency, mining variability remains high, hence the focus on operational excellence.
For this reason, mining has long had a preference for quickly following technologies in other sectors. However, the technologies mining requires, particularly in loading and hauling, are quite different from applications in other sectors.
Mining reshapes local geography, for example, so key elements of infrastructure need to be moveable. Equipment engines are also very large and operate at full power for 20 to 40 percent of their life span.
Operational hours are often 24/7/365 with no charging windows, battery cycling rates are 10 times those of other sectors, and ambient conditions are generally unfavourable.
In this new paradigm, mining will need to lead on innovation, but this is starting to happen through major investments in technology, with examples including Anglo American and Fortescue Metals Group (FMG).
Do you have any tips on decarbonisation strategies and solutions?
TC: In the near term, miners should target productivity improvement to reduce diesel carbon waste. This is highly cashflow-positive and helps sites achieve production schedules. However, most sites will need new high resolution data systems.